编者按:智能制造是我国加快建设制造强国的主攻方向,而智能工厂是推动智能制造的切入点和突破口,也是制造业数字化转型的重要载体。近日,本市公布了《上海市100家智能工厂名单》。上海核电系统共有上海发电机厂、上海汽轮机厂、凯士比核泵、昌强重工、阿波罗机械、上海森永6家单位成功获评。为了总结和分享上海核电企业智能工厂的建设经验,我们将分期对以上6家智能工厂进行专题报道。
昌强重工:自主开发数字化管理平台,数联智造构建重型装备锻造透明工厂
智能工厂简介
上海昌强重工机械有限公司(以下简称“昌强重工”)位于临港新片区,专业从事大型、超大型多向模锻液压机的研制及各类大型装备结构件的锻造业务。2017年研制出世界首台36000吨超大六向模锻液压机,为我国基础工业领域关键部件的自主化提供了重要支撑。
昌强重工积极响应国家推动产业数字化转型号召,针对重型装备锻造企业离散型生产管控需求开发的智能化解决方案—CIS透明工厂系统,实现了工厂级数字孪生,为昌强重工的快速发展提供了有力支持。
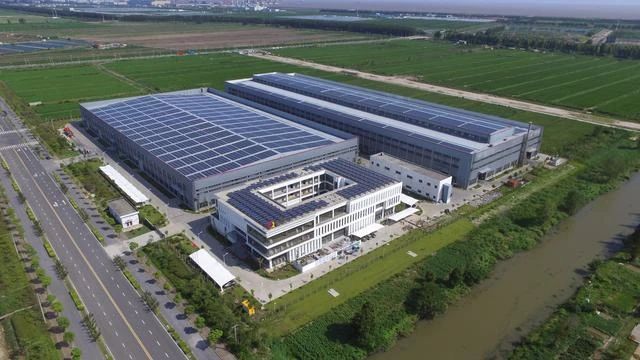
全方位一体化数据平台管理系统
昌强重工独立自主研发的数字化智能工厂管理系统(CIS),集成了整套设计、生产、制造,管理、物流、财务、人事等企业经营管理模块,采用多种实时传感系统、测控设备、实验室数据采集技术、3D可视化技术、大吨位上下料机械手、锻件自动测温等智能装备,实现制造过程的自动化和网络化、物流采集信息化,形成“有高度(战略)、有深度(现场)、有宽度(全方位)”多维度集成的数字化管理模式。
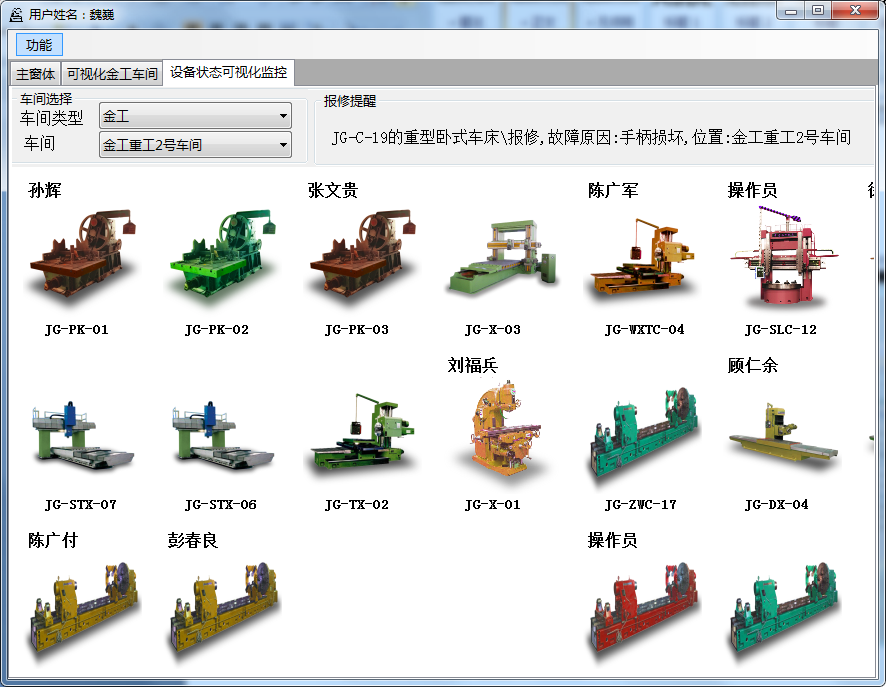
全3D仿真数字孪生透明工厂
昌强重工基于WebGL 3D展现技术,对工厂实景实物进行建模,将厂房、设备、生产过程、人员派工、能耗等信息实时投射在虚拟的三维空间中,初步实现了制造过程的自动化和网络化、物流采集信息化的3D可视化数字孪生工厂。
同时,智能工厂搭建了业务中台和数据中台提供数据支持,业务中台通过将工厂内各实际业务抽象为WebApi的方式,实现工厂内部及外部系统间的业务流程交互及数据交互;数据中台通过数据源、数据标准、数据质控三方面对智能工厂的数据进行数据治理。
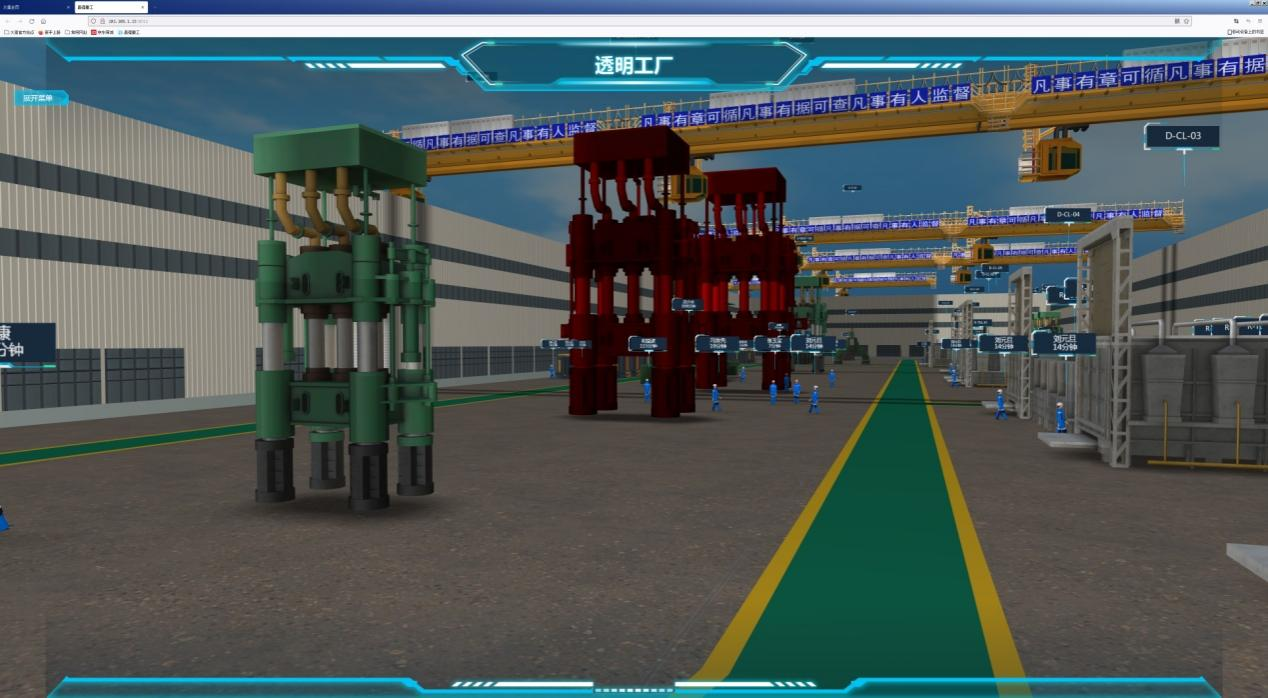
全流程虚拟锻造平台
基于QForm平台的全流程虚拟锻造系统融合了虚拟制造、设计制造一体化等先进理念。主要包括基础配置、工艺数据知识库、标准库、模板库和问题库。将整体生产制造过程数据,结合专业化设计、知识库应用、数据闭环等系统流程化管理功能的应用,实现内部专家库的PDCA的循环,不断扩展优化底层数据,推进最优工艺。让每一位工程师摆脱“个人经验”限制,充分利用企业技术资源,全面协同工作。
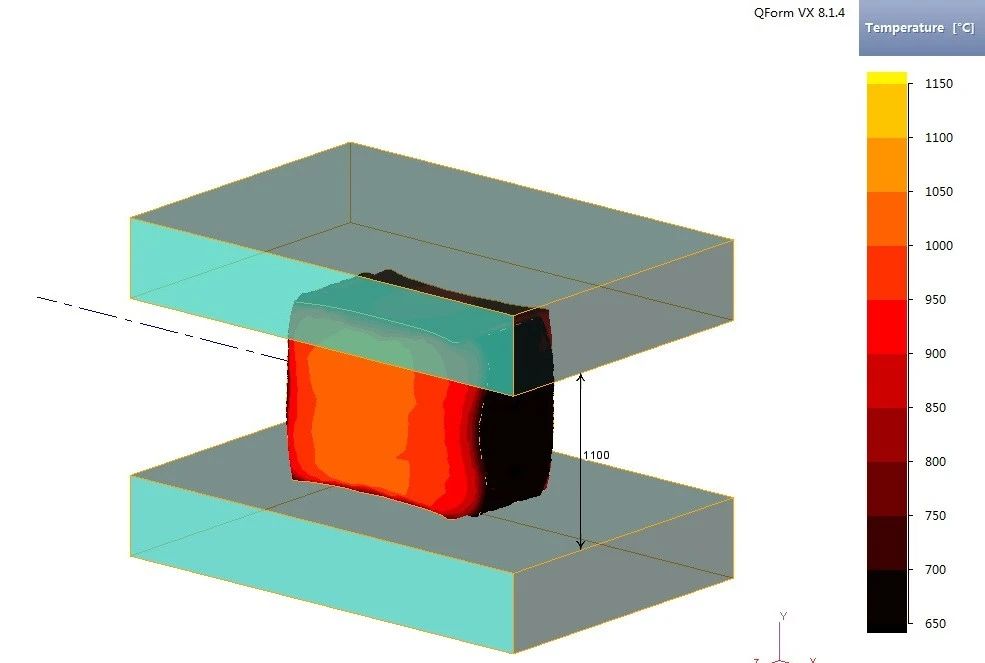
智能工厂成效
昌强重工以“转变发展方式、变革制造模式、引领行业进步”为数字化转型目标,基于全面数字化管理平台,与虚拟制造、智能制造系统有机融合,实现了全方位多维度集成的数字化管理模式,在智能制造、智能管理方面取得了一定成效。
智能制造方面,基于工厂级数字孪生,配合昌强重工自主研发的多向模锻压机建立的数字孪生体,实现了锻造过程的前期设计仿真、模拟生产,实际生产过程中的实时监测与控制,产品全数字化质量控制与追溯及数字化交付。
智能管理方面,随着透明工厂前期积累数据的不断深化应用,昌强重工关键经营指标相较系统投产前有了明显的提升,产品一次质量合格率从86.0%提升到93.7%;订单的按期交付率提升7.3%;订单的平均交付周期从58天缩短至40天,能源利用率提升2.9%。